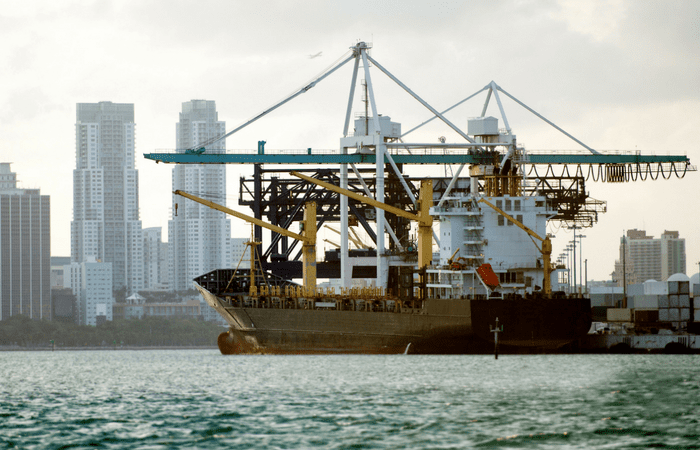
A discussion about what lead up to the West Coast port closures, and how supply chains were affected.
Written by: Kelly O’Riley, Director of Freight Forwarding Services & Matt Collins, Director of Freight Forwarding Sales
Introduction | Printer Friendly PDF
Every six years, the U.S. West Coast ports negotiate and renew their labor contract with the International Longshore and Warehouse Union (ILWU). In 2002, a dispute caused major delays and port shutdowns. Again in 2014, protracted labor negotiations caused slowdowns and shutdowns throughout the West Coast. However, additional external factors in effect in 2014 caused a ripple effect of delays, congestion, and even loss of product to the entire U.S. supply chain.
With approximately 45 percent of all U.S. imports passing through the 29 West Coast ports and representing 12.5 percent4 of the GPD, the congestion had a crippling effect on retailers during the holiday season. Early estimates place the national cost of the congestion at as much as $7 billion in 20152 alone.
Third-party logistics provider MD Logistics mobilized to help its clients stay apprised of port conditions and choose the best course of action, taking cost and type of cargo into consideration. As the crisis comes to a close, MD Logistics reflects on ongoing industry factors that will continue to cause delays and how importers can anticipate and prepare for future congestion scenarios.
The Issue
At midnight on July 30, 2014, the ILWU and Pacific Maritime Association (PMA) labor contract expired without resolution. As peak season began in July and extended into the fall and winter, ILWU members instituted slowdowns at the ports of Los Angeles and Long Beach, the nation’s busiest seaport. The two ports serve as a hub for West Coast imports, transferring $1 billion worth of cargo each day, primarily goods from Asia5. While ports utilized overtime hours to meet the demand and many believed the crisis would resolve by the holiday season, congestion quickly grew.
Negotiations continued through the winter. In February 2015, the crisis peaked as all 29 West Coast ports instituted multi-day shutdowns before negotiators finally reached a deal on February 20.
Los Angeles and Long Beach handle 70 percent of the commodities that come into the U.S. from Asia. Imports from Asia to these ports typically require two to three days to be unloaded and transferred inland. At the peak of the labor crisis, transfer inland was taking up to four weeks, with backlogged container ships sitting idle off the coast. Total transit time from Asia to the U.S. across the Pacific increased from 16-18 days to 28-35 days.
The Ripple Effect
To work around the Los Angeles and Long Beach congestion, some freight forwarders began sending cargo to alternative ports including Seattle, Tacoma, Prince Rupert, Vancouver, and Oakland. As a result, congestion and transit time ballooned in these areas as well. In August 2014, Prince Rupert port in British Columbia announced that it would turn away any U.S.-bound cargo, causing additional transit time for cargo that had been redirected there and causing further congestion in nearby Seattle and Tacoma.
In congested ports, predominantly Los Angeles and Long Beach, temporary labor that was brought in to service the backlog was unskilled and ineffective at operating the cranes. Whether an importer decided to stay put or reroute its cargo, all incurred extra costs in storage, demurrage, port congestion fees, and more.
When cargo finally reached shore, Midwest importers needed to determine how to make up the time that they had already lost in the remaining transit. Some chose trucks, as opposed to rail, to send commodities to the Midwest, as the rail system was congested as well.
During the slowdowns and shutdowns, terminals such as Chicago had thinned their operations, staff, and equipment due to the slow influx of cargo. When the dispute ended in February, the container yards needed to regain capacity very quickly, and soon began receiving 75-100 percent more cargo than normal as the commodities waiting in the Pacific began coming in quickly. Normally, during the spring-time, transit time from Chicago to Midwest inland points takes two days. However, in the early spring of 2015, transit times along that route increased to four or five days. Overall, Midwest transit times increased by approximately 40 percent during the nine-month crisis period.
Guiding Clients through the Port Delays
As MD Logistics, a third-party logistics provider based in Plainfield, Ind. saw the early warning signs of the delays in the summer of 2014, they began discussions with each of their clients who might be affected by the congestion and advised them to ship as early as possible, or redirect to alternative ports. MD Logistics provided direct updates from the ports to its clients and walked them through various scenarios and alternatives available to them. The options for clients were:
- Redirect to alternative West Coast ports. Importers redirect shipments to West Coast ports other than Los Angeles and Long Beach. Due to the backlog, congestion grew at these ports as well.
- Redirect to the East Coast. Importers redirect shipments through the Panama Canal to unload cargo at ports on the East Coast. Costs for redirecting to the East Coast are typically 30-40% higher, and reliability was uncertain as some East Coast labor unions threatened to honor the strike for cargo redirected from the West Coast.
- Redirect to the Gulf Coast. Importers redirect shipments to Gulf Coast ports such as Houston. On top of the increased costs of going through the Panama Canal, Gulf Coast ports are often tied up with congestion from the oil and gas industries in the area.
- Use Air Freight. Importers use air freight to import high-priority cargo. Airfreight can often times cost upwards of three to four times the amount of ocean freight, so this option is in most cases cost-prohibitive.
- Wait it Out. Importers keep their shipments berthed in the Pacific until the congestion clears.
Although MD Logistics did assist several clients in redirecting high-priority cargo into alternate ports including Baltimore, Norfolk, and Seattle, for most clients it found that staying put and waiting out the congestion on the West Coast was the best option in terms of reliability and cost.
In one case, a client had 150 crates with specific labeling requirements for retail distribution. MD Logistics was able to implement a plan to bring the crates into Seattle, unload the products and utilize truck / Intermodal carriers to avoid the ocean container rail congestion. The time savings were substantial for the client and costs for the change in process only increased 5 – 10%. MD Logistics provided weekly condition updates on the ports and provided the client guidance and recommendations on the go. The move provided an immediate benefit to the client’s supply chain.
Unlike smaller logistics providers, MD Logistics was able to effectively support clients through its many locations and partners throughout the country, with the flexibility to bring imports into smaller ports and adjust quickly to the port delays and closures with transportation alternatives.
“We kept our clients informed and apprised of every option available to them so they could make the most educated decision,” said Matt Collins, Director of Freight Forwarding Sales. “What differentiates us from our competition is our ability to over-communicate with our clients and to walk alongside them.”
Compounding Factors
Outside of the labor dispute, additional factors compounded the overall congestion, and will continue to be an issue even as delays from the labor dispute wind down.
- Container Chassis Shortage. For broader economic reasons, many ocean carriers and steamship lines phased out their container chassis service lines by 2014. During the recession, 40 percent of the U.S. trucking capacity left the market, of which only half has returned. Without this convenient service of provided container chassis, port truckers must now either rent or buy their own6. As companies scrambled to catch up with the backlogged orders, there was a shortage of container chassis to rent.
- Appointment Delays. One new movement in the transportation market is that terminals now require an appointment to retrieve shipments. During the west coast port closure crisis, some port truckers would wait all day for an appointment, only to find that there was no equipment available and that they needed to return the next day. Although the appointment system was instituted to alleviate delays, it ended up having the opposite effect.
Conclusion
Although the labor dispute is formally resolved until the next labor contract negotiation period in 2020, delays are still in place from the nine-month saga. The East Coast labor contract is up for renewal in 2017, which could lead to additional congestion.
The newly-created appointment system and chassis shortage for truckers will continue to cause delays as capacity within the transportation industry has not returned to its pre-recession levels.
Most mid- and large-sized companies affected by the crisis had the inventory size and budgets to weather the crisis, but many small companies did not have the expertise to navigate freight forwarding on their own, relying heavily on third-party logistics providers such as MD Logistics. Retailers with delayed holiday shipments and perishable products were hardest-hit by the crisis.
Experts estimate that the congestion from West Coast port closures will be alleviated by June 2015—just in time for peak season to begin again in July. The economic impact and operational ramifications of the port slowdowns and closures will continue to ripple throughout the logistics industry through 2015.
Resources
- “Los Angeles and Long Beach Port Congestion and Delays – The Facts, Causes and Solutions,” American Export Lines. https://www.shipit.com/blog/los-angeles-and-long-port-congestion-and-delays-the-facts-causes-and-solutions/
- “West Coast port closure could cost $2.1 billion per day,” Puget Sound Business Journal. https://www.bizjournals.com/seattle/morning_call/2015/02/west-coast-port-closure-could-cost-2-1-billion-per.html
- “West Coast port congestion could cost retailers $36.9 billion in the next 24 months,” Kurt Salmon. https://www.businesswire.com/news/home/20150207005007/en#.VS0pBZTF8Uh
- “The National Impact of a West Coast Port Stoppage,” National Association of Manufacturers and the National Retail Federation. http://www.supplychain247.com/paper/the_national_impact_of_a_west_coast_port_stoppage/national_association_of_manufacturers
- “West Coast closures are hitting several industries hard,” NPR. https://www.npr.org/2015/02/14/386199926/west-coast-port-closures-are-hitting-several-industries-hard
- “Q&A: Port Truckers Face Future Without Carrier Chassis,” Journal of Commerce. https://www.joc.com/content/qa-port-truckers-face-future-without-carrier-chassis