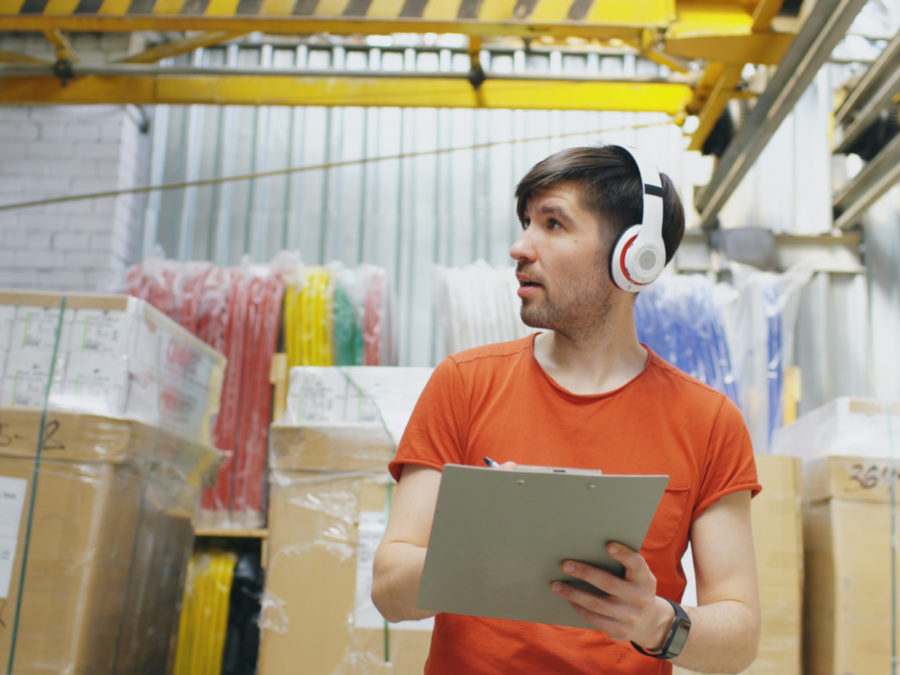
Supply chains are going digital — and not a moment too soon.
The coming of e-commerce and the omnichannel has ignited a revolution in the way that goods get to market. For consumer products companies, the old model of manufacturer to wholesaler to retailer is no longer adequate to meet the needs of buyers.
Online shoppers today want one-day, same-day and even same-hour delivery. In response, suppliers and carriers must shift from relying solely on full truckloads and pallets to enabling the delivery of small packages to homes and businesses. That’s not possible to achieve with traditional distribution networks. The old way of processing orders and accompanying data is simply too slow, costly and inefficient to service a direct-to-consumer world.
Enter the digital supply chain, a concept that encompasses and integrates all business processes required for the selling of products: design, planning, engineering, manufacturing, logistics, warehouse management, transportation and customer service.
Each of those disciplines has historically functioned in isolation, requiring the manual replication of data and often resulting in big gaps in communication. To tear down those walls, companies need to begin transforming their supply chains, with the goal of achieving customer centricity.
Every business claims to be “customer-focused,” but what does it really take to earn that description? Companies must move beyond the age of mass production and consumption. True customer centricity requires the ability to design supply-chain processes to service a customer segment of one.
The digital supply chain holds the key. Think of it as a representation of the physical world — a “digital twin” that provides a high-level view of operations. Companies gain visibility over key processes, enabling them to fulfill and deliver orders with unprecedented speed. Manufacturers pivot from selling products to delivering a broad array of solutions and services. And logistics providers move from physical to digital inventory, as they adopt such cutting-edge technologies as 3-D printing.
For planners, it’s more than a question of improving forecasting accuracy. The digital supply chain enables producers and logistics providers to capture demand signals from both structured sources (orders and point-of-sale data) and unstructured sources (sentiment analysis, predictive algorithms and the growing use of machine learning). That latter category of data is unobtainable in an analog world.
Digital technology enables process automation enterprise-wide, along with the ability to manage by exception. Call it the “touchless” supply chain — one that frees humans from mundane, repetitive tasks, and greatly reduces the potential for errors and delays in the transmission of information.
Successful implementation of a digital supply chain requires the adoption of predictive business processes that reflect customers’ ever-changing demands. No longer can manufacturers turn out large lots of product and hope that they catch on in the marketplace. By creating a digital twin of physical operations, companies can tweak product all the way back to the design stage, in line with actual demand and consumer preferences.
Technology plays a crucial role in the migration to a digital environment. Companies need to adopt smarter, automated systems across all areas of the supply chain. Manufacturers, for example, can replace continuous production lines with flexible cells that are deployed in a near “plug-and-play” setting. Over time, the cells become smarter, with the ability to route product automatically to the next stage of production.
Additional new technologies arising from digitization include artificial intelligence, machine learning, robotics and 3D printing. All have one element in common: they allow for far greater flexibility in the configuration and targeting of product to consumers.
Digital twins have already proved their worth in the area of maintenance and service. By employing lightweight model visualization to create the virtual representation of an asset in the field, and capturing data from sensors embedded in the asset, service providers can gain a complete picture of actual performance and operating conditions. They can also use asset intelligence to simulate real-world environments for predictive maintenance.
For companies struggling to understand and address consumer trends today, the name of the game is visibility. A digital twin of operations fulfills that requirement across a broad network of partners, manufacturing facilities and distribution centers; smart assets and products under your control; vehicles in transit carrying products and materials; traffic patterns and weather activity; and demand signals derived from sentiment analysis, point-of-sale data and product trends.
The digital supply chain has arrived. It’s time for companies to start thinking about their supply chains in a completely new way.
Hans Thalbauer is senior vice president of digital supply chain and industry 4.0 for SAP.
Source: Supply Chain Brain