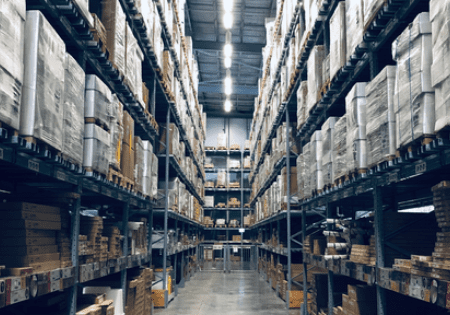
With warehouse space tightening because of the ongoing e-commerce boom, it is essential to know the difference between a fulfillment center and a distribution center.
As consumers become more comfortable purchasing larger items online, the need for warehouse space has skyrocketed. According to CBRE Group, the U.S. availability rate for industrial real estate is at a mere 7 percent. Space is especially tight in high-demand areas near urban centers.
Meanwhile, every $1 billion in e-commerce sales requires 1.25 million square feet of warehouse space, according to data from CBRE.
Both fulfillment and distribution centers provide services that are needed for customers to determine whether a product is in stock or not. The amount of complexities that surrounds warehouse operations during the e-commerce boom is outstanding. However, organizations that support multi-channel distribution have the challenge of monitoring shipments all the way to the final mile.
You may be left wondering whether you need a distribution center or a fulfillment center. And what exactly is the difference between the two?
Fulfillment Centers
According to ShipBob, a fulfillment center relies on a third-party logistics provider (3PL) to fulfill customer orders on behalf of e-commerce retailers.
With the advent of e-commerce, fulfillment centers came into existence to get online orders to customers in a timely fashion. Amazon has helped drive the necessity of fulfillment centers, operating more than 75 locations across North America, as of November 2018.
Now, micro-fulfillment centers—a small-scale warehouse close to the end consumer—located near city centers are relieving some e-commerce companies, such as Amazon, from managing this process by taking control of last-mile delivery.
An essential part of the supply chain
Fulfillment centers are a crucial part of the supply chain as they help to get online orders to consumers. Typically owned by a third-party, fulfillment centers help retailers strategically store their goods so that workers can quickly pick orders after an online purchase is completed.
Fulfillment centers ship orders directly to an individual consumer’s home and can process high volumes of products for both B2B and B2C customers.
Retailers who use fulfillment centers rely on the third-party to complete the picking process. In addition, the third-party provider manages the inventory to ensure that the right products are stocked and negotiates rates with shipping carriers.
With fulfillment centers, optimization, planning and communication with carriers have to be more streamlined so that packages aren’t delayed. Truckers and warehouse workers will have to work closely together to ensure customer satisfaction, because the consumer touch point is no longer in stores.
Distribution Center
BusinessDictionary.com defines a distribution center as a facility that is used for receipt, temporary storage and redistribution of goods according to orders as they are received.
A distribution center serves as a bridge between the supplier and its customers. It efficiently houses products and is used to meet the growing standards of shipping.
Walmart, the largest retailer in the country, had 173 distribution centers in 2017, according to MWPVL. The chain operates on 775 million square feet of retail space, requiring over 900 million square feet in warehouse space.
All about the customer
Distribution centers are customer centric, serving the retail store directly. They are typically owned by the retailers that occupy the space; however, leasing is becoming a more popular option.
Distribution centers are an essential part of the order process and are typically more complex to manage as more products are stored there. According to SupplychainMinded, the centers are more likely to be equipped with the latest technology to make order processing more efficient. In addition, distribution centers are more likely to have warehouse management systems (WMS) and transportation management systems (TMS) in place.
Suppliers typically ship products to distribution centers, which assist retail locations as needed. For example, when you order an item from Walmart online and choose to pick it up in store, the nearest distribution center will oversee it.
Connecting the Orders to the Consumer
Fulfillment centers and distribution centers are similar in that they both want to get products to the consumer as fast as possible. In the end, it’s about customer experience.
“More and more, customers are embracing online orders, so it’s not simply about passing those orders downstream and fulfilling them more quickly. It’s about injecting data and insights from warehouse operations into the buying process,” says John Bruno, vice president of product management at Elastic Path. “It’s about providing the buyer an accurate count of inventory at the time of purchase so orders don’t get cancelled. It’s about connecting inventory, location, shipping options and customer preferences to fulfill orders when and how the buyer wants them. It’s a whole new level of personalization, but on the plane of warehouse operations.”
Source: Supply & Demand Chain Executive