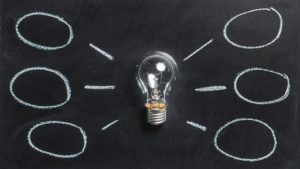
While the biggest issue for 2021 remains the rollout of a viable vaccine, the manufacturing industry is looking to re-invent itself in preparation for the remainder of the twenties.
2020 was not what any of us expected. Unprecedented disruption from the Coronavirus disease (COVID-19) pandemic, an unusual presidential election and a period in which the manufacturing industry rose to the challenges presented by innovating and creating solutions.
But, what does this all mean for 2021, and what will be the big industry drivers in the “New Normal” post-pandemic world?
First and foremost, it’s worth mentioning that the manufacturing industry has been through a great deal this year and has come through with impressive resilience and determination, a real testament to the creativity and passion of those in the industry. Many companies have used 2020 to push digital transformation initiatives, having seen their traditional processes lacking through the crisis. Others have developed new offerings and solutions to assist in the fight against COVID-19.
While the biggest issue for 2021 remains the rollout of a viable vaccine, the manufacturing industry is looking to re-invent itself in preparation for the remainder of the twenties, a decade which, despite a bad start, will likely be the most innovative in human history. And, let’s not forget that come January there will be a new President in the White House. Beyond these major impacts, here are four of the drivers coming in 2021:
A focus on the value and sustainability of supply chains
After a historically disruptive year, OEMs are waking up to the fact that the measure of a supply chain is much greater than its landed costs.
As chief supply chain officers consider their supply chains in a post-pandemic world, they will look more toward TCOO (total cost of ownership) and the additional value that is often overlooked, such as time-to-market, agility to adapt and change quickly and resilience against disruption.
Additionally, in 2021 the sustainability of the supply chain will become more important than ever. As consumers are becoming increasingly concerned with where things are made, the impact on the environment and the kind of companies they buy from, this will in turn lead brands to consider these issues when selecting their supply chain and manufacturing partners. IDC predicts that by 2025, 90% of the global 2000 will mandate the use of reusable material in hardware supply chains.
Investment in Made in America
There are numerous dynamics right now driving the debate around where parts and products are made. The election of Joe Biden as President has sharpened focus on this, while the pandemic has shone a light on the frailties of some supply chains as well as an over-dependence on certain countries or regions. In fact, the 2020 State of Manufacturing survey showed that 73% of OEM leaders have minimized, or have plans to minimize, reliance on China.
Politicians are seeing local manufacturing as a policy that will create jobs and boost economic recovery; America’s strength has always been its technological innovation. The emergence and adoption of new digital manufacturing technologies has the potential to make the United States a leader in manufacturing once again, but this will require appropriate investment on training and education to ensure skill shortages don’t stifle recovery.
The switch to demand-led NPI
For decades the manufacturing industry, and in particular the electronics manufacturing sector (EMS) sector, has had an “if we build it, they will come” approach to growth. They have focused on creating impressive capacity, particularly in lower cost geographies, but the truth is this model is much more about utilization.
As digitally enabled manufacturing ecosystems develop, manufacturing is moving to a demand-led solution where brands can select factories, geographies and even manufacturing and fulfillment methods from the elastic capacity available in the market.
The democratization of digital and the failure of Industry 4.0
Industry transformation has overwhelmed and confused while simultaneously filling column inches and occupying hours of boardroom discussions, but what has been achieved? Industry 4.0 has felt like too much talk and not enough action and we’ve not really seen any digital dividend.
Fictiv’s 2020 State of Manufacturing Report found the vast majority of companies are looking to accelerate digital transformation, yet a small percentage had well thought out, well-funded plans. Digital manufacturing ecosystems are now making it possible for companies large and small to reap the dividends of digital transformation, without huge upfront investment in internal solutions.
Create, innovate and thrive, not just survive
All in all, the world in 2020 was very different to the world in 2019, and it seems likely that 2021 will provide a chance to reset, bringing the best of the past together with the innovative approach of this year and the technological possibilities of the future.
The industry will need to be ready for change, from the c-suite to the shop floor. Nations like the United States will need to ensure they have the workforce training and STEM education in place to create the skills needed for the future, even if we don’t know exactly what that future might be. This means investment in education and infrastructure.
In the c-suite, it’s a case of disrupt or be disrupted, create, innovate and don’t just survive, but thrive in the new post-pandemic normal.
Source: Supply & Demand Chain Executive