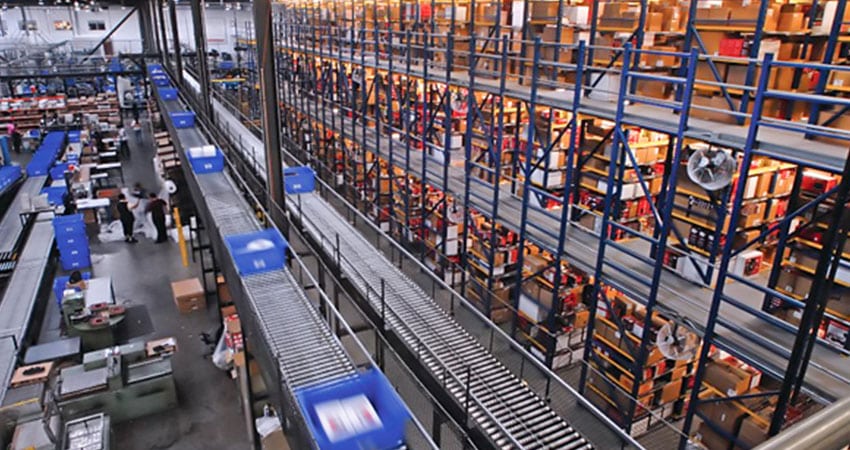
Your company’s ecommerce fulfillment center is running out of space. You have been tasked with determining whether the existing facility can scale up to the five-year business plan, or a new facility is required.
In many markets, commercial space is extremely limited and expensive. According to Cushman & Wakefield, the average national industrial vacancy rate was 4.1% in the third quarter of 2021, the lowest on record back to 1995. At the same time, the firm reported average rents rose 8.3% to $7.18 per square foot.
Below is a checklist of the major requirements you need to consider in evaluating both your existing and potential new ecommerce fulfillment facilities:
Do Your Homework Before a Site Visit
Before you start a real estate search for space, determine the requirements for the fulfillment needed to meet your company’s business plan. For most companies, this requires considerable amount of data collection and crunching. This homework upfront is crucial to determining how long any facility will meet the business needs.
Quantify Current Storage Space
The starting point is to identify the square footage and cubic space of the current facilities and ancillary spaces. This may sound simple, but many companies are using multiple smaller bulk facilities; storing pallets on trailers in the yard; or using short-term rental space. Understand the space needs for all functions, not just product storage.
Where does the existing facility fall short of space needs or flow? Our blog on assessing ecommerce fulfillment centers will help you in this evaluation.
Future Capacity Needs
Your business plans are generally at a high level and in dollars of sales, inventory and turn. However, from a fulfillment perspective, to calculate bulk and forward picking storage size and locations, you will need the number of SKUs, value of inventory for average weeks and peak weeks, inventory turn, planned SKU growth and typical percentage of stock that is obsolete.
Are there any changes to the product mix that radically affects space? How many bays of pallet rack storage are required and can be accommodated by a building’s clear span?
Once you have current cubic and square footage for the potential building, identify how many years does the facility need to last before another move or expansion?
Department Space Requirements
It is important to think about the space allotment in addition to storage. For inbound receiving space, you’ll need the profile of the incoming shipments (average and peak), the number of cases, pallets, and containers received, space for QA tasks and space to stage product awaiting put away.
For outbound shipping space, profile the number of shipments per month (peak and average), types of shipment (small package, pallet, LTL, etc.), and by carrier. Space is needed for package accumulation for specific carriers.
Current Shortcomings and Wish List Items
Where does the existing facility fall short of space needs or flow? Would the process be much more efficient if a change in product flow happened in the new facility? Is additional space needed for custom racking that would be beneficial based on your inventory?
It’s important to have items you’d like to have to help differentiate facilities that can all seem similar. One may be just better than another because it offers something on your wish list.
Facility Assessment
Transportation: What is the proximity and access to ports, highways and carrier hubs? Does the yard have sufficient space to drop/store trailers? Does it have required security? For safety, does the site’s traffic flow separate trucks from visitors and employees?
Receiving and shipping dock doors: It can be cost prohibitive to add doors. How many dock height doors vs. ground height dock doors are needed? Is there enough for inbound, outbound and dedicated doors for trash or staged pallets?
Building shape and product and order flow: Footprints which are odd shapes can create inefficiencies as compared to a more standard-shaped building. How will inbound product flow from receiving docks, staging, QA to bulk reserve, returns processing and value-added operations? How will forward picking, order fulfillment and shipping be laid out?
Use of cubic space: What is the opportunity to go vertical with product storage vs. a larger footprint and lower ceilings? What is the clear span for storage, and the maximum number of pallets you can stack? Consider building codes for sprinkler clearance from the product. What is the column separation and aisle width that maximizes pallet rack capacity?
Condition of floors: Are the floors in good condition? Can they support pallet rack weight? Having issues with the floor can limit material handling and automation.
Equipment and robotics: What types of sortation, picking modules, and robotics will be employed? What are the positives and negatives at this facility for automated equipment? You can see this prior post to learn how companies are employing automation to reduce labor.
Other facility requirements: The following items should not be overlooked:
- Lighting, electrical and communications service
- Forklift charging stations and power requirements
- Maintenance and equipment rooms
- Meeting rooms
- Training rooms
- Conference rooms
- Employee lunchroom and break rooms
- Bathrooms (size for number of employees)
- IT server rooms
- Space for supplies by type and proximity to the packing area
Future expansion: How many cubic feet and square feet does the expansion allow? Is there sufficient acreage for the building expansion, parking and truck traffic?
As you review available facilities, is staying in the existing location and improving productivity and improving storage capacity a viable option? The homework above gives you the target goals by year.
Detailed planning by year is crucial to determining whether a potential new location or upgrades to your existing ecommerce fulfillment center will be your best option.
Source: Multichannel Merchant